Making connections for 60 years
Bringing originality to original equipment manufacturing
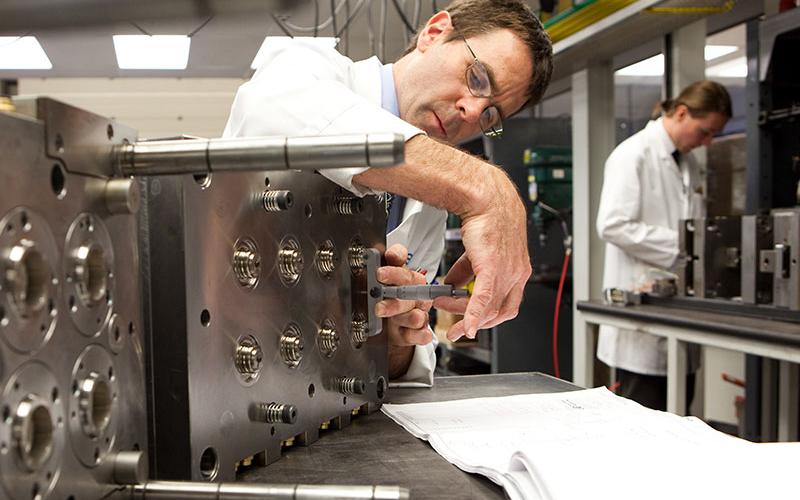
Since 1961, John Guest’s pioneering innovations have been transforming performance and efficiency for many industries. Back in the 70s, John Guest invented push-fit technology that revolutionised the way connections are made.
Market leaders and niche players have been using our technology for decades to solve the key challenges they face. Why? Because the clever science behind our technology ensures optimal performance, longevity and fast and simple installation.
From distilling wine to hydroponic farming to animal feeding equipment, environmental test chambers and fuel cells, the OEM applications are endless.
Precision engineering and world-class quality
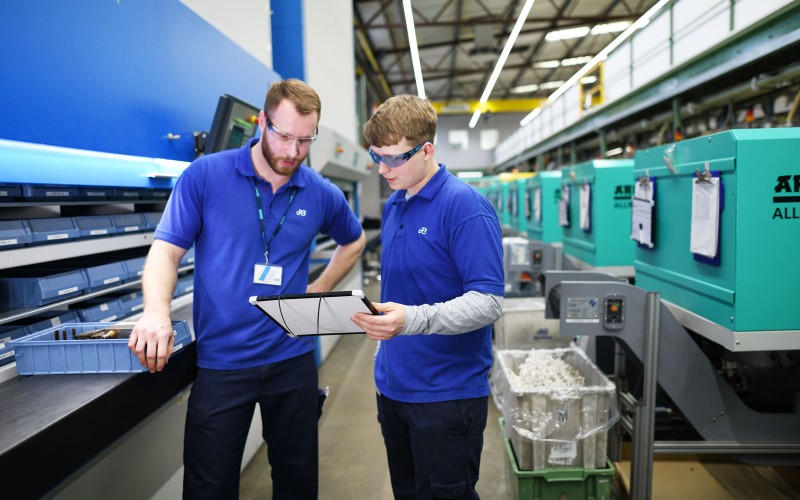
Innovative design is at our core. It means clever, time-saving solutions for you, engineered with lasting quality you can rely on.
From state-of-the-art R&D to world-class product testing and quality control, our innovations are the by-product of pure engineering mastery. The same ethos drives our customer service and design capabilities, ensuring we provide expert support whenever you need it.
Suitable for air, vacuum and fluid applications, we offer an extensive range of push-fit solutions including cartridges, fittings, tubing and valves.
Benefits of John Guest push-fit technology for OEMs
Bespoke solutions to individual specification
Reliable push-fit connection technology
Quick and easy assembly
Low insertion level and high burst pressure
Soft metal or plastic housing materials
Global expertise with local technical support
Bespoke solutions for OEMs
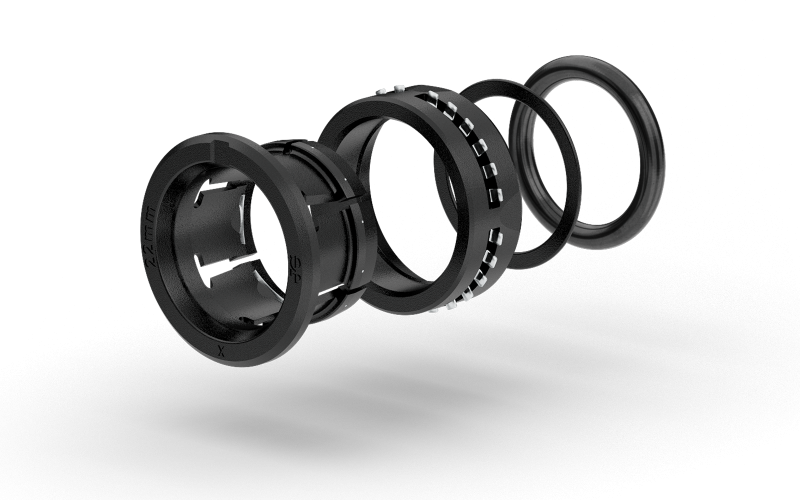
Blending engineering and manufacturing expertise with a high-quality service enables John Guest to develop customised solutions to meet the needs of many different customers.
By working in close partnership with you, we integrate our push-fit technology into your own branded products. From initial concept to CAD design, prototype testing through to full production, our teams are on hand to provide expert advise and support every step of the way.
Here are some examples of the type of projects we get involved in.
Learn more about our OEM solutions by downloading our brochure.
Here’s to the next 60 years
We’re proud of what we’ve achieved over the past 60 years, and our engineers are focused on many more innovations to come. Our most important innovation ever? The next one, of course.
Made in the UK. Trusted worldwide.
Find out about the other industry sectors we support and why we've been trusted for 60 years.